【事例付き】ブルウィップ効果とは
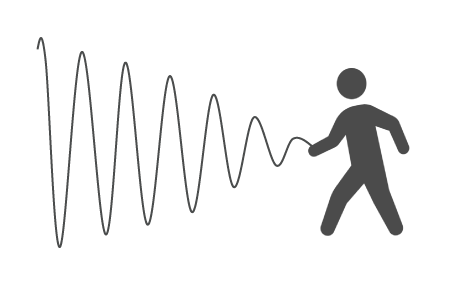
SCMにおいて多くの企業の頭を悩ますブルウィップ効果。
企業間の問題として取り上げられているケースが多いですが一社の中でも発生し得るものです。
今回は例を交えてブルウィップ効果の原因や影響、解決策についてご紹介します。
(”効果”というと、日本語ではポジティブな意味にとらえられますが、Bullwip Effectの”Effect”は何らかの事象によってもたらされる”影響”や”結果”を意味します。)
目次
ブルウィップ効果とは
ブルウィップ効果とは、サプライチェーンの川下の需要変動が川上にいくほど増幅していく需要変動現象です。
川下のごくわずかな需要変動が拡大しながら川上へ伝わっていく様子が、ムチを鳴らしているように見えるためブルウィップ効果(鞭効果、Bullwhip Effect)として世の中に広まりました。
新型コロナウィルス感染症(COVID-19)の拡大によって、ワクチン、消毒液、マスクの需要が急激に増えたため、コロナ需要が落ち着いたときの在庫過多や欠品が心配されていました。ブルウィップ効果の起源はシステムダイナミクスの生みの親であるジェイ・フォレスターの『Industrial Dynamics(産業のダイナミクス)』(1961年)にあります。そのため、当時は「フォレスター効果」として知られていました。
ブルウィップ効果の例
下の図1は、「サプライヤー ⇒ メーカー ⇒ 卸売業 ⇒ 小売業」というサプライチェーンに対してブルウィップ効果がどのような影響を与えるかのイメージ図です。自社の、「営業部 ⇒ 調達部 ⇒ 生産部」に置き換えても同様のことがいえます。
図1.SCにおけるフェーズ別のブルウィップ効果
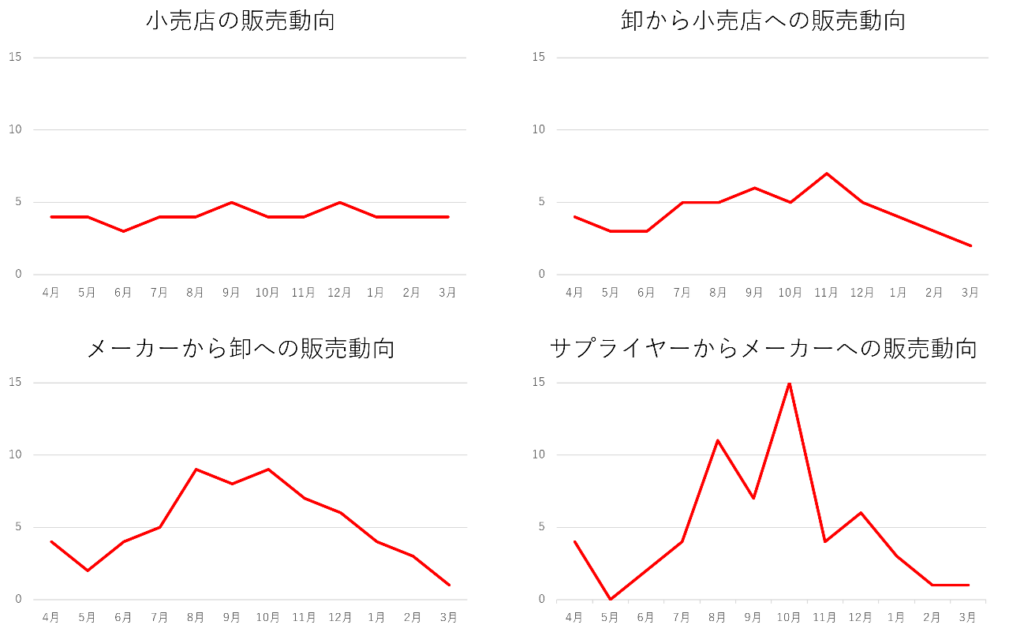
このように、川下の小売店から川上のサプライヤーにサプライチェーンをさかのぼるにつれて販売動向のばらつきが大きくなっていきます。
また、下の図2のように、小売店とサプライヤーの販売動向を比較すると、実際の販売実績とはかけ離れた計画が立っていることが分かります。
図2.川上と川下のずれ
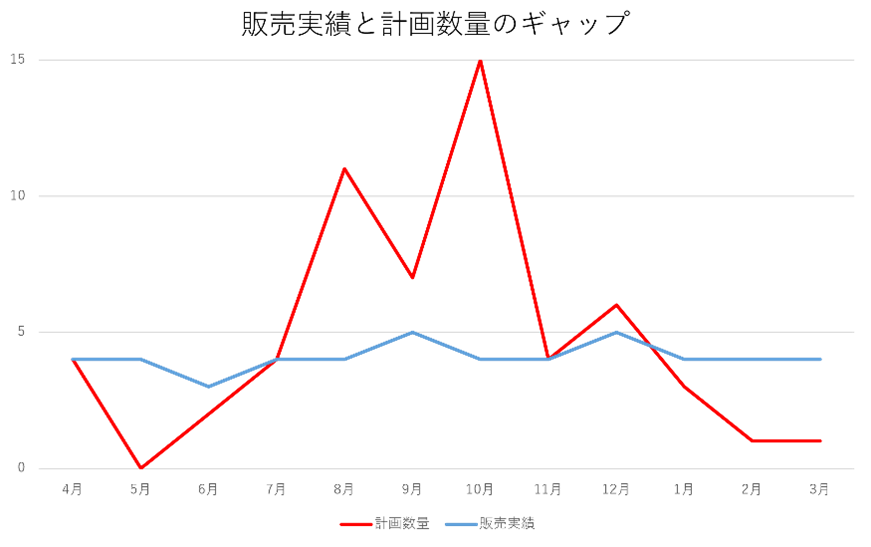
(図1、2はブルウィップ効果の影響をわかりやすくするためにサンプルの数値で計算しています。)
ブルウィップ効果の原因
ブルウィップ効果の原因は以下の3つがあります。
需要予測の精度
商品の販売数量、販売タイミングを正確に予測することができていないためブルウィップ効果が発生します。
しかし、消費者ニーズの多様化やライフサイクルの短期化など、需要予測を難しくする要因は多くあります。さらに、災害の発生やSNSによる口コミの拡散によって想定外の需要変動が誘発されることもあります。そのため、需要予測の精度を100%にすることはできませんが、統計的手法やAIを活用することで精度をできる限り高めることはできます。
意思決定者の数
意思決定者が多くなればなるほどブルウィップ効果が発生するリスクは高くなります。
企業間では、「小売業 ⇒ 卸売業 ⇒ メーカー ⇒ サプライヤー」、企業内では、「営業部⇒ 調達部 ⇒ 生産部」のように、複数の組織と意思決定者がいます。それぞれが独自の都合や思惑をもって意思決定に関わることで、小さな需要の変動が大きな波動になります。また、欠品や過剰在庫を恐れる担当者の心理も波動を大きくする要因となります。
情報の透明性・スピード
企業間、組織間で情報の連携ができていない場合や情報伝達が遅いことが発生の原因になります。
例えば、小売店で起きた需要変動の原因をメーカーが把握していない場合、実績値による予測しか行うことができず、いつまで変動が長引くのかが分からない状態が続きます。さらに、意思決定者が増えることで情報伝達のタイムラグが発生し、川上へいくほど情報の誤差とタイムラグが大きくなる危険性が高まります。また、調達・供給リードタイムが長くなればなるほど需要の変化に対する計画の不確実性が高まります。
ブルウィップ効果がビジネスに及ぼす影響
ブルウィップ効果が発生すると、サプライチェーン上にいるすべての企業、組織に大きな悪影響を及ぼします。
過剰在庫によるコスト増
実際に販売される量よりも多くの調達・生産計画を立ててしまうことで、在庫金額の増加や無駄な調達・生産が行われるため、多大なコストが発生してしまいます。それだけではなく、無駄な廃棄や生産が増えると環境問題にもつながります。
欠品による機会損失
実際に販売する量よりも少なく調達・生産計画を立ててしまうことで、欠品が発生し、本来得られたはずの収益を逃してしまいます。また、欠品を起こしてしまったことで取引先からの信頼を失うことにもつながります。
生産ライン稼働率の悪化
自社で生産ラインを持っている場合、需要の変動に大きな波動が起きると、生産ラインの稼働にばらつきが発生します。忙しく稼働する時期とあまり稼働しない時期が波のようにやってくるため、生産ラインの稼働が非効率的になります。その結果、人や材料を持て余してしまったり残業代の増加につながります。
ブルウィップ効果の解決策
サプライチェーン上のそれぞれの時点で売れた分だけ発注・生産することができれば、理論的にはブルウィップ効果は発生しません。ブルウィップ効果を抑制するためには、できるだけ川下の需要の変動の規模と原因を正確に把握する必要があります。
SCM(サプライチェーンマネジメント)
サプライチェーンに関わる全ての企業、組織のモノ・お金・情報の動きをリアルタイムに共有する考え方のことをSCM(サプライチェーンマネジメント)といいます。ブルウィップ効果だけでなく企業の利益を高める上で非常に効果的なのですぐに実践しましょう。
ジャスト・イン・タイム・生産方式(JIT生産方式)
トヨタが開発したジャスト・イン・タイムは、すべての工程が後工程の要求にあわせて「必要なときに、必要なものを、必要なだけつくる(調達する)」方法のことです。元々はトヨタ工場内で活用されていましたが、研究が進み、企業間において実現するケースも現れました。企業間でジャスト・イン・タイムが実現できれば、サプライチェーン上の川下の企業が必要としている量だけを必要なだけつくることができます。
ただし、リアルタイムに川下の企業の需要量を把握している必要があり、なおかつ要求された量を素早く柔軟に生産することは困難であるためあまり有力ではありません。
企業統合
サプライチェーン上で、自社より川下に当たる事業者を買収・合併することで、ブルウィップ効果の影響を最低限に抑えることができます。企業統合をすることで、例えばメーカーが小売までできるようになれば、実販売量をとらえた調達・生産計画を立てることが可能となります。
メーカーが小売まで行っている実際の例としては、ZARAやユニクロなどのSPAが代表的です。SPAは、素材調達から、商品の企画、生産、販売までのすべての工程を一貫して行うアパレル企業のことをいいます。ブルウィップ効果を抑制するだけでなく、卸売業者などの流通の中間マージンが発生しないため、コストカットが期待できます。
まとめ
ブルウィップ効果について調べると、企業間をテーマにして書かれている記事が多いためあまり実感を持ちにくいですが、実際は皆さんが仕事をしているすぐそばで起きています。具体的には、営業部⇒調達部⇒生産部の場合や、自社販売拠点⇒本社調達部⇒海外工場の中でブルウィップ効果が起きているケースがあります。しかしながら、多くの場合はブルウィップ効果に対して有効な取り組みがされていません。ひどい場合は、発生していることすら認識していないこともあります。さまざまな解決策のなかでもSCM(サプライチェーンマネジメント)がもっとも有効かつインパクトが大きいため、実践/見直しをしてみてはいかがでしょうか。