事業拡大を妨げる問題を解決。操作性の大幅改善で全ての関係者がメリットを実感
概要
斗山(Doosan)重工業は、韓国の斗山企業グループに属する総合重工業企業で、発電設備、プラント設備、インフラ設備などの生産を手掛けており、サウジアラビア、インドなど海外で大型のプラントや発電所建設を担うグローバルEPC企業です。
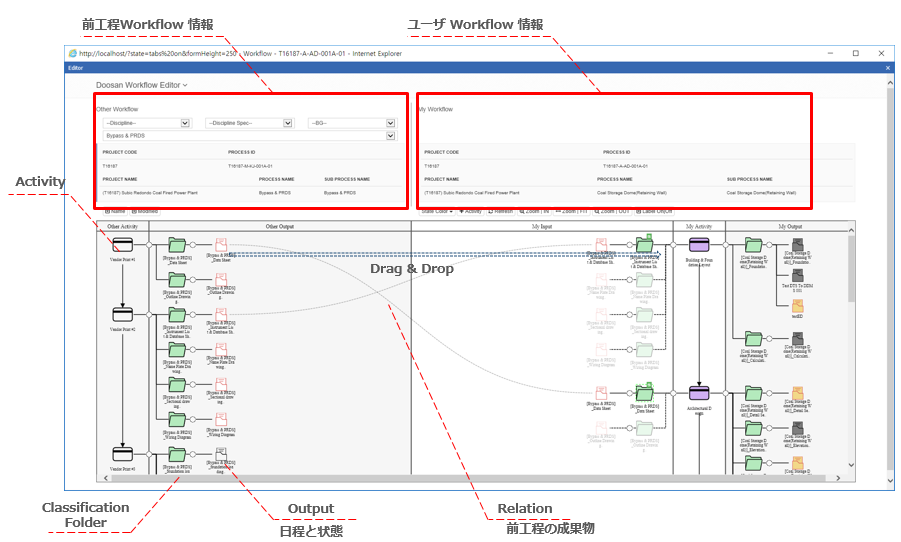
導入背景及び目標
斗山重工業の発電所施設やタービン設計開発業務は個別受注設計でなされており、多種にわたるエンジニアリングデータの分散化、設計プロセスの属人化、設計の日程計画が見えないなど、事業拡大を妨げる問題を抱えていました。コスト競争力を維持するためにも業務の効率化と品質の担保が必須ですが、案件の拡大や厳しい法規制を遵守するためにプロセスは複雑化し、個人のスキルや工夫に頼らざるを得なくなっている状況下で、従来の部品組み立て方式をサポートするPLMシステムの適応は難しいものでした。そこで将来の変化を見越して、拡張性と柔軟性が保証されるArasのプラットフォームをベースに、SI開発方式でシステムを構築することにしました。
まず、設計手順を正確に遂行するための「設計プロセスの標準化」を目的とし、そのためにプロジェクトタイプに応じて標準のプロセスを定義し、これを標準ワークフローテンプレートとしてデータベースに管理するようにしました。ワークフローのタスクは、Aras InnovatorのアドオンであるDynamic Task Manager を利用してプロジェクトの日程計画へ連携して定義され、ガントチャートは日程計画の共有のために使われるようにします。
次に、機器や設備の仕様情報を体系的に管理するために、エンジニアリングデータベースを活用し、機器や設備の標準の分類を定義し(設備テンプレート)、それぞれにスペック情報とモデリングの情報が付与され、機器のライブラリとなり、この情報をインポートして3Dモデリングが作成されます。機器ごとに管理に必要な属性の値が付与され、リストや項目単位でアクセス権も設定されます。
対象となる事業が大きいため、約10か月間の一時開発の後パイロット案件に適用し、4か月後に施行を完了、本格稼働を開始しました。その後は既存システムとの連携を行いながら徐々に事業別に対象を広げて展開中です。
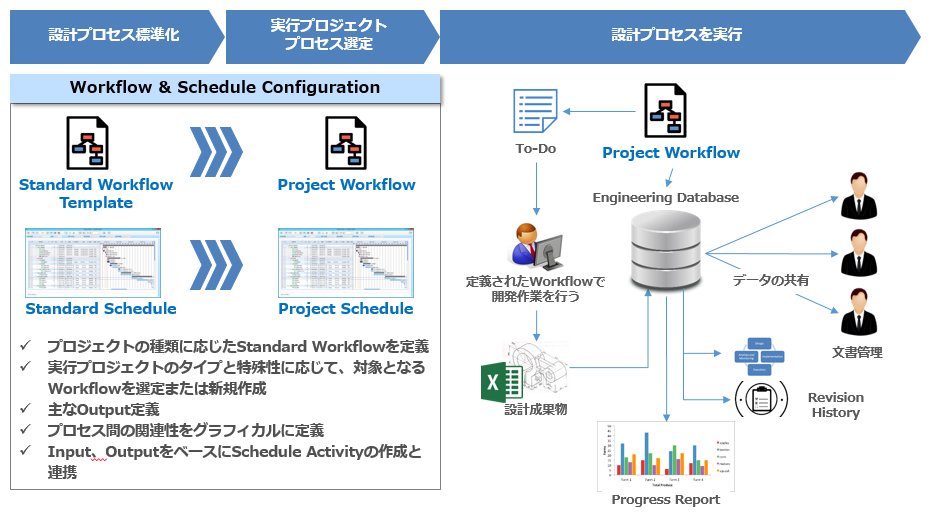
構築の効果
ワークフローを定義し、業務プロセスを標準化したことで、統合設計環境の骨子が構築されました。ワークフローに沿った設計プロセスの実行を徹底するため、全てのユーザが抵抗なく利用できるように、操作性の良いワークフロー定義の描画機能・グラフィカルな管理画面でアクティビティと成果物を関連付けるEditorを開発し提供しました。それにより、業務の手順が可視化され、直感的に業務の状態と文書との関連性とを把握することができるようになりました。
機器ライブラリとエンジニアリングDBの活用により、仕様情報が体系的に管理できるため、3Dモデリングにより必要な資材や設備の数量が計算され、設備の調達や施工、生産の元データとなるほか、類似プロジェクトの見積もりに再利用することも可能でした。
エンジニアリングポータルにより、関係者がタイムリーに最新情報を共有することができ、設計の整合性を向上させることができるようになりました。全ての関係者はこのポータルページを介して、送達/依頼手続き・データ登録が可能で、自分に関連する情報が常にニューフィードとしてアップデートされ、プロジェクトのステータスもダッシュボードで確認ができます。
現在、広範囲なポートフォリオに対応するため、更にSCMとの連携も進めています。