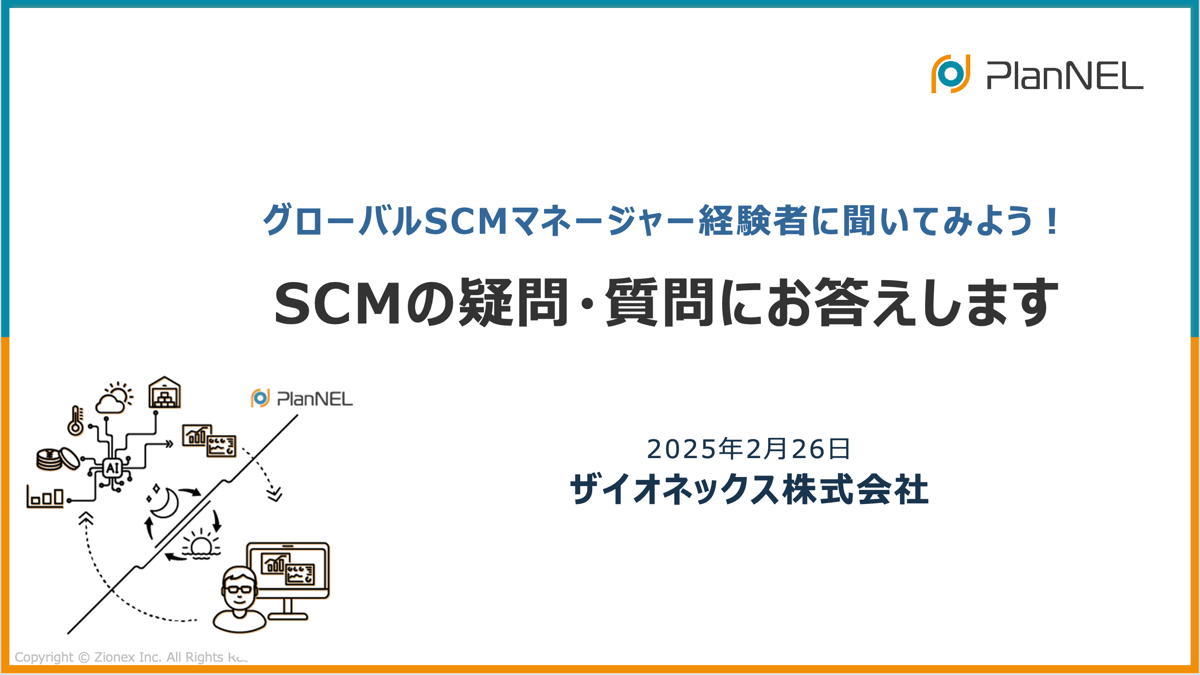
安全在庫と発注点 4つの計算式
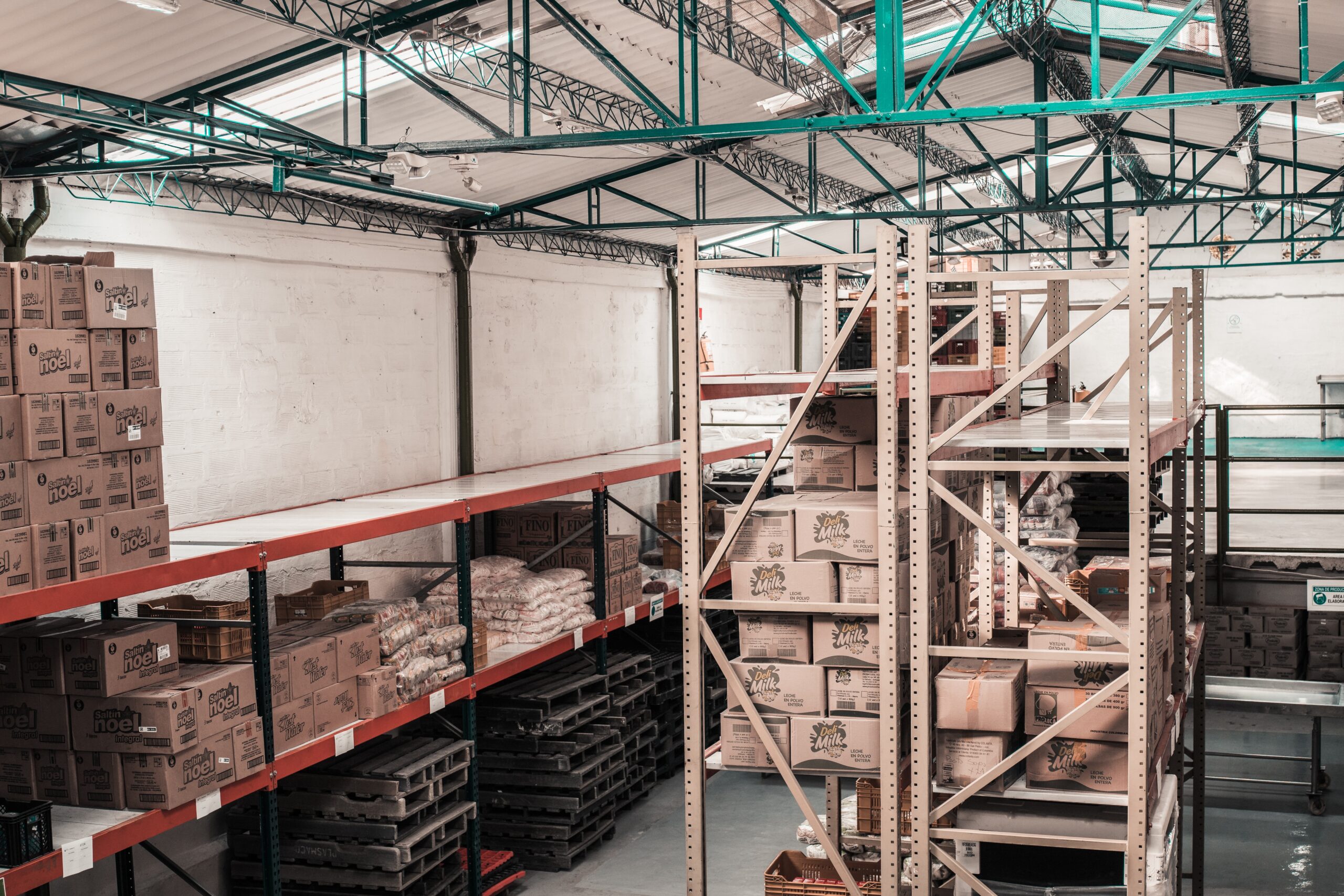
これまでの経験や勘に頼って発注する数量を決めていませんか?発注数量を計算する方法は多くありますが、自社の製品にどの式が当てはまっているかは実際に計算してみないとわかりません。ここでは、Excelで算出が可能な計算方法を4つ紹介します。
安全在庫とは
安全在庫とは、不確実な需要変動に対して欠品を起こさないための最低限の在庫数のことです。不確実な需要変動とは、季節性、流行などによって需要が増減することをいいます。また、リードタイムの変動も含みます。
不確実な需要変動
製品によって様々な需要の変動があります。例えばティッシュや洗剤などの生活必需品と呼ばれるものは安定した需要がありますが、傘の場合は、雨が降ったときや梅雨の時期に大きく需要が増加します。したがって、ティッシュよりも傘の方が、不確実性が高いためより多くの安全在庫を持っておく必要があります。
不確実なリードタイム
日本国内で生産し日本国内に輸送する場合は、大きな事故や災害がない限りリードタイムに数か月単位の大きな変動は起きないでしょう。しかし、ベトナムで生産しイギリスに輸送する場合は、事故や災害に加えて、輸送方法、関税、など変動要素が多くなります。したがって、リードタイムが変動する可能性と変動の幅が大きくなります。
安全在庫はこういった不確実な需要とリードタイムをカバーする在庫のことをいいます。
発注点とは
発注点とは、発注を行うタイミングのことをいいます。具体的には、在庫が一定の数を下回った時点で発注を行う基準となる在庫数のことを指します。例えば、発注点を3,000個とした場合、在庫数量が3,000個を下回った時点で発注を行うことになります。SCMの標準が浸透している海外では、Reorder Point(再発注点)と呼ばれることが一般的です。
4つの安全在庫と発注点の計算式
安全在庫を求める計算式は複数あります。自社製品や自社の発注体制、発注先の制約を考慮し、最も適している計算式を活用しましょう。
安全在庫日数
古くから使われており、最も簡単な計算方法です。販売の頻度が少ない製品や、販売数量が少ない製品に対して有効な計算式です。
例えば、1日あたりの平均販売数量が100個、平均リードタイムが30日である場合に、15日分の安全在庫を持ちたい場合、次のような計算を行います。
安全在庫日数 計算式
安全在庫=平均販売数量×安全在庫日数
例:安全在庫=100個×15日=1,500個
安全在庫が分かった後は、どのタイミングで発注すれば良いかという発注点を求めます。
発注点 計算式
発注点=安全在庫+平均販売数量×LT
例:発注点=1,500個+100個×30日=4,500個
図1は、これまで計算した内容を図にしたものです。1,500個の安全在庫があり、4,500個が発注点となっています。つまり、在庫が4,500個になると1,500個の発注を行います。仮に1日の間に4,000個を出荷すると、在庫が2,000個になり、その時点で4,000個の発注を行います。この計算方法単独ではABC分析による製品分類や目標*サービスレベルを考慮していません。ABC分析のC分類に対して適用されるケースが多く、〇日分の在庫を確保しておきたいという狙いがある場合に使用します。
図1.安全在庫日数

*サービスレベル:1から欠品許容率を引いた値(1-欠品許容率)です。言い換えると100回のうち何回欠品を許すかということです。例えば、サービスレベルを95%とした場合、100回のうち5回の欠品を許容するということになります。また、安全在庫の計算にサービスレベルを利用するためには、欠品許容率を安全係数に直す必要があります。
Max-Ave
Max-Aveは、需要の最大値から平均値を差し引いた値を安全在庫とする考え方です。具体的には(最大販売数量×最大リードタイム)-(平均販売数量×平均リードタイム)となります。
サンプルとして以下の図2,3のデータを使用します。
図2.販売数量
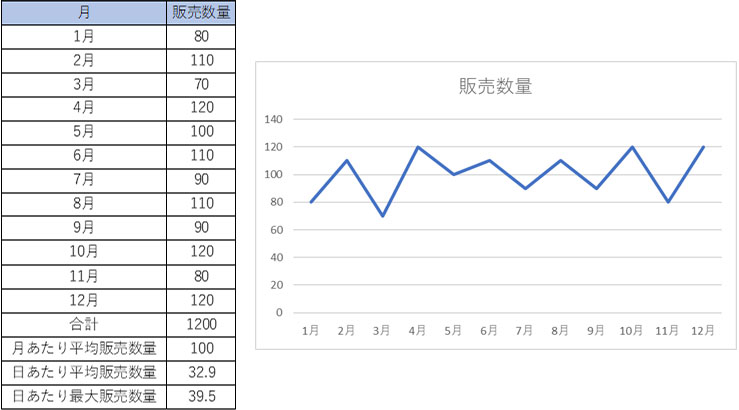
図2では、12か月間の販売数量の合計が1,200個、1か月あたりの平均販売数量は100個、1日あたりの平均販売数量は約33個、1日あたりの最大販売数量は約40個です。
図3.リードタイム
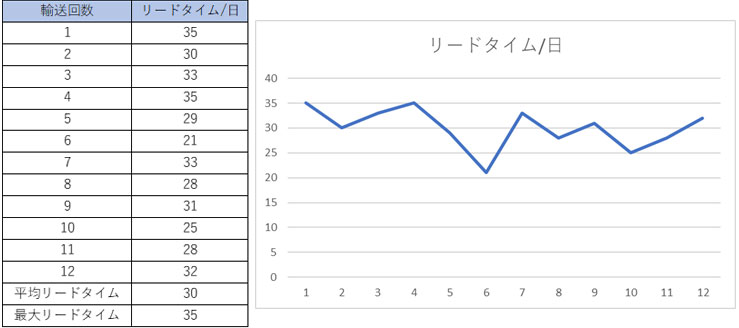
図3では、12か月間に12回(毎月1回)の輸送があり、平均リードタイムは平均30日、最大リードタイムは35日です。
図2、3を計算式に当てはめると次のようになります。
Max-Ave 計算式
安全在庫=(最大販売数量×最大リードタイム)-(平均販売数量×平均リードタイム)
例:安全在庫=(40個*35日)-(33個*30日)=425個
次に発注点を求めます。計算式は前回と同じです。
発注点 計算式
安全在庫+平均販売数量×LT
例:発注点=425個+33個*30日=1,415個
Max-Aveは販売実績とリードタイムが分かってさえいれば計算できる簡単なものです。しかし、リードタイムや販売実績データの中に、平均値から大きく外れた異常値が含まれていると計算結果に影響を及ぼします。異常値がある場合は、あらかじめ平均値に直して計算することをおすすめします。また、安全在庫日数計算と同じく、Max-AveもABC分析による製品分類や目標サービスレベルを考慮していません。
需要の不確実さを考慮した安全在庫
安全在庫の計算式で最も標準的な計算方法です。需要を不確実なものとして捉え、需要の標準偏差から安全在庫数を導き出します。例として、図4のデータを使用します。
図4
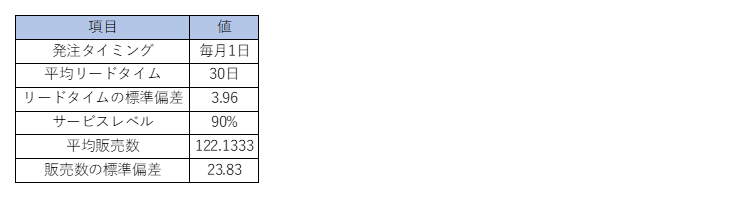
※ここでは販売数を活用していますが、出荷実績であっても問題ありません。需要の実績データであれば計算式に活用することができます。
サービスレベルを90%とした場合、安全係数は約1.28となります。
需要の不確実さを考慮した安全在庫 計算式
計算式:安全在庫=安全係数×販売数の標準偏差×√(LT+*CT)
例:安全在庫=1,28*23.83*SQRT(30+30)=237個
*CT:サイクルタイムの略。発注してから次の発注までの期間。発注周期ともいいます。仮に1か月を30日とし、毎月1日に定期的に発注している場合は、CTは30日となります。
次に発注点を求めます。計算式はこれまでと同じです。
発注点 計算式
安全在庫+平均販売数量×LT
例:237個+122個*30日=3,901個
この安全在庫の計算式は多くの在庫系システムに取り入れられており、需要のバラツキが多い場合に有効です。一方でリードタイムにバラツキが多い場合は次の計算式が有効です。
リードタイムの不確実さを考慮した安全在庫
需要予測や販売計画の精度は高いが、リードタイムが安定しない製品に対して有効な計算式です。リードタイムを不確実なものとして捉え、リードタイムの標準偏差を考慮した安全在庫を算出します。リードタイムのバラツキが大きいほどリードタイムの標準偏差が大きくなります。例として再度、図2,3のデータを使用します。
図2(再掲) 図3(再掲)
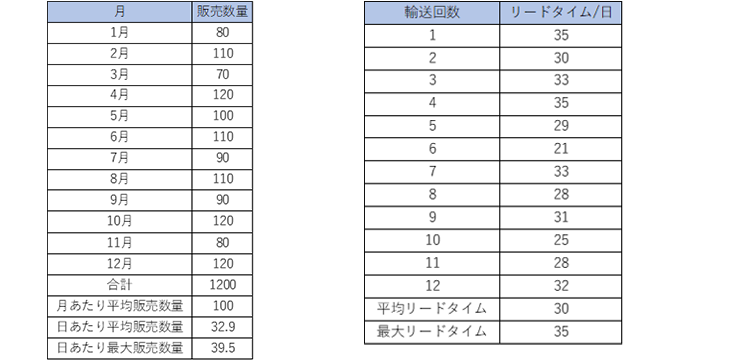
リードタイムの標準偏差は図4の3.95を使用します。
リードタイムの不確実さを考慮した安全在庫 計算式
安全在庫=安全係数×平均販売数量×リードタイムの標準偏差
例:安全在庫=1.28*100*3.95=507個
次に発注点を求めます。
発注点 計算式
安全在庫+平均販売数量×LT
例:507個+100個*30日=3,507個
海外生産品や海外輸出品など、入庫日が見通しにくい製品はLTのバラツキが大きくなる傾向があるため、こちらの計算式が適しているでしょう。
まとめ
本記事で紹介したすべての計算方法はエクセルで簡単に計算することができるため、ぜひ自社製品の実データを使って計算してみてください。SKUが数百であればExcelでも計算可能ですが、数千、数万になる場合は在庫計算システムの導入をおすすめします。ただし、計算式で算出した数は絶対的に信頼できる数とは限りません。日々の需要に応じて在庫の持ち方は大きく左右されるため、季節性による変動や災害などがある場合はその都度対処する必要があります。また、安全在庫数を計算する前にABC分析を行った上で、製品ごとにどれくらいのサービスレベルを設けるかが非常に重要となります。